Further underlining its commitment to improve the industry’s environmental footprint, specialist greeting card printer Windles has invested inautomated paper banding machinery with the aim of eliminating plastic secondary packaging that has historically been used for cards in transit to retailers.
The Windles Group has a target to remove another five million pieces of plastic, further reducing the environmental impact of the greeting card industry and the adoption of its new automated Paper Band process will take it closer to achieving this goal.
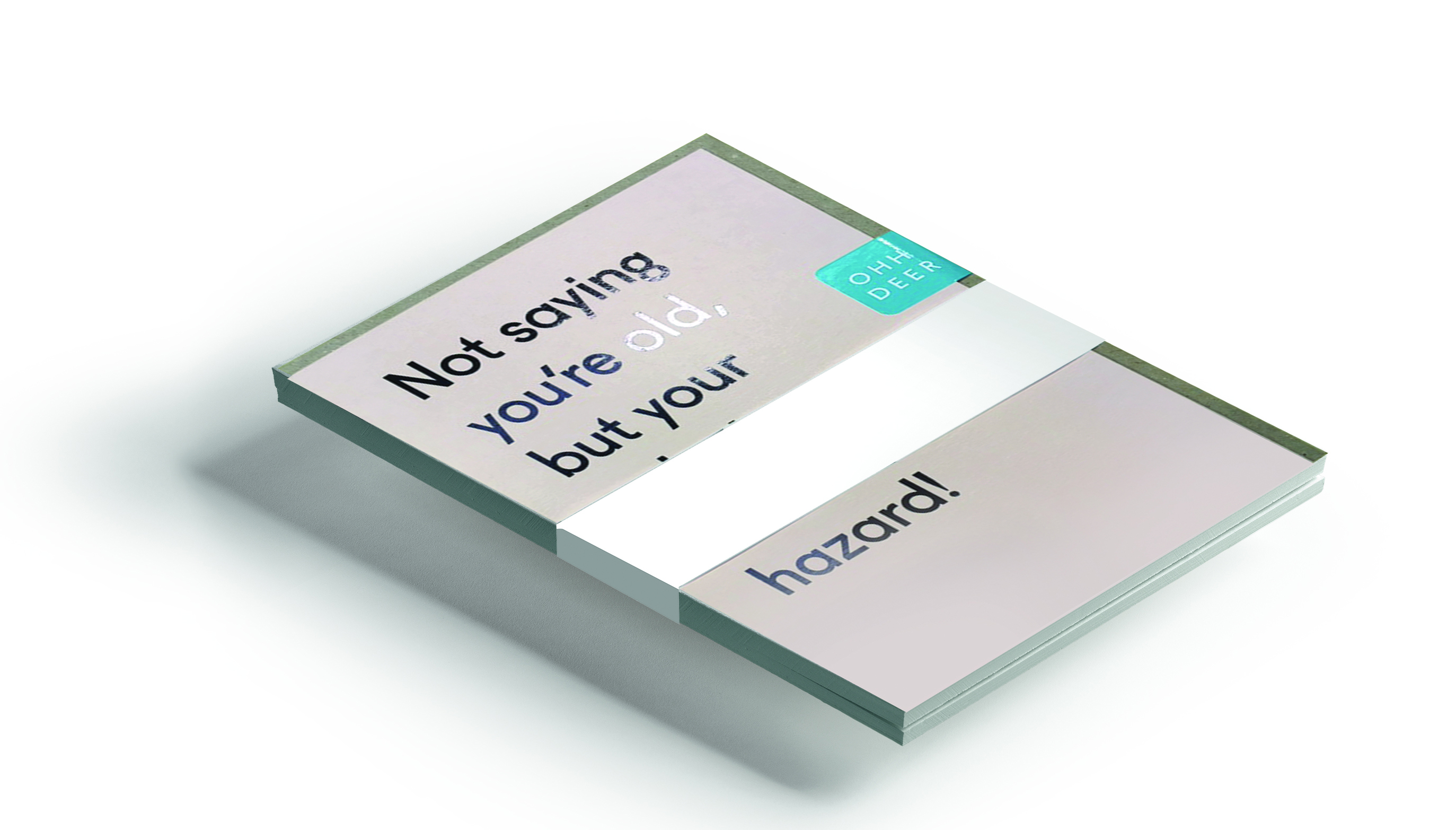
“We must all congratulate ourselves in the greeting card industry with the incredible switch to alternative methods of primary packaging during the past two years,” highlights Bruce Podmore, managing director of Windles. “Some 85% of product previously packed in a plastic cellobag, have now been replaced by a ‘naked’ solution,” he added.
While accepting that not all retailers or publishers, largely for protective reasons, do not wish to go ‘naked’ with all their cards, Windles feels that there is environmental ground to be gained on the secondary packaging front.

“This is the hidden plastic the end customer doesn’t see,” Michelle Mills, business development and marketing manager of Windles told PG Buzz. “It makes no sense for us as an industry to put a strain on our fragile planet by cellowrapping cards and/or including secondary plastic banding when there is no need, with paper banding offering a solution for the latter. We do of course recognise the need for some product to be wrapped. So ideally if we had a magic wand, we would see that all of the local councils have the infrastructure and recycling facilities in place to recycle the 100% OPP plastic used for greeting cards. It is a frustration for us that at industry level the plastic wrapping is recycled and put to good use.”
Windles has invested in multiple paper-banding machines which means it can now offer a fully automated process to wrap a paper band around publisher’s greeting cards to unitise them ready for distribution to retailers.

“It’s long been our mission to provide our customers with the most innovative techniques to enable them to bring their creative ideas to life while also ensuring their products are produced in the most environmentally sustainable way,” stressed Michelle. “Our Incada campaign has already made a saving of over 250,000 kg CO2 emissions – by switching our stocked one-sided coated GC1 board to one made in Cumbria, rather than using those sourced previously from India, China and Canada. We pioneered Kard Klasp as a plastic-free option for primary packaging when there is a requirement to keep the envelope secured safely inside the card – this has so far eliminated the use of 20 million pieces of single use plastic,” she quantified.
Several publishers have already taken the decision to move to using Windles’ Paper Bands, with many more on the verge of making the shift.
“We embrace change that is right for our customers and right for our industry. It is our aim to remain ahead and by working together we can do it,” reinforced Bruce.
Top: The logo for Windles new Paper Band process.